Porosity in Welding: Identifying Common Issues and Implementing Best Practices for Prevention
Porosity in welding is a prevalent problem that commonly goes undetected up until it triggers significant problems with the integrity of welds. In this discussion, we will discover the crucial aspects contributing to porosity development, analyze its damaging results on weld efficiency, and go over the finest practices that can be taken on to lessen porosity event in welding processes.
Common Sources Of Porosity

Another regular perpetrator behind porosity is the visibility of contaminants on the surface area of the base metal, such as oil, grease, or rust. When these contaminants are not properly removed before welding, they can evaporate and come to be trapped in the weld, causing flaws. In addition, using dirty or wet filler products can present contaminations right into the weld, adding to porosity problems. To minimize these typical reasons of porosity, comprehensive cleansing of base steels, correct protecting gas option, and adherence to ideal welding specifications are crucial practices in attaining top notch, porosity-free welds.
Influence of Porosity on Weld High Quality

The presence of porosity in welding can significantly compromise the structural integrity and mechanical homes of bonded joints. Porosity creates voids within the weld metal, weakening its overall toughness and load-bearing capacity.
Welds with high porosity degrees often tend to display reduced impact stamina and decreased ability to warp plastically prior to fracturing. Porosity can hinder the weld's capability to effectively send forces, leading to early weld failing and prospective security threats in crucial frameworks.
Finest Practices for Porosity Prevention
To boost the architectural stability and top quality of welded joints, what certain actions can be applied to decrease the occurrence of porosity during the welding process? Making use of the appropriate welding technique for the specific material being bonded, such as changing the click this welding angle and weapon position, can even more avoid porosity. Regular evaluation of welds and instant remediation of any type of issues determined during the welding procedure are important methods to protect against porosity and create high-grade welds.
Relevance of Correct Welding Techniques
Executing proper welding techniques is critical in making sure the structural integrity and top quality of bonded joints, constructing upon the structure of reliable porosity avoidance actions. Welding techniques directly affect the overall stamina and toughness of the bonded structure. One crucial element of appropriate welding strategies is preserving the proper warm input. Too much warm can cause increased porosity because of the entrapment of gases in the weld swimming pool. Alternatively, insufficient heat may result in insufficient blend, creating possible weak points in the joint. In addition, using the appropriate welding specifications, such as voltage, present, and travel speed, is crucial for attaining audio welds with marginal porosity.
Moreover, the choice of welding process, whether it be MIG, TIG, or stick welding, need to align with the particular demands of the job to make sure optimum results. Proper cleansing and prep work of the base metal, along with picking the ideal filler product, are likewise vital parts of skillful welding techniques. By sticking to these best methods, welders can decrease the danger of porosity development and generate premium, structurally audio welds.
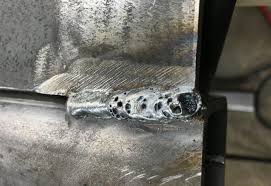
Evaluating and Quality Assurance Measures
Testing treatments are important to detect and prevent porosity in welding, guaranteeing the stamina and durability of the final item. Non-destructive testing approaches such great post to read as ultrasonic screening, radiographic testing, and aesthetic inspection are typically employed to recognize potential issues like porosity.
Post-weld inspections, on the various other hand, analyze the last weld for any kind of defects, consisting of porosity, and validate that it satisfies specified standards. Carrying out an extensive quality control plan that additional reading includes complete screening treatments and examinations is paramount to minimizing porosity issues and making sure the overall high quality of welded joints.
Verdict
In conclusion, porosity in welding can be an usual concern that influences the high quality of welds. By recognizing the typical sources of porosity and implementing ideal practices for prevention, such as proper welding strategies and screening actions, welders can make certain top quality and trustworthy welds. It is important to focus on prevention approaches to reduce the event of porosity and preserve the stability of bonded structures.
Comments on “What is Porosity in Welding: Secret Aspects and Their Impact on Weld Top Quality”